Michael: Sure. FactoryView is part of our SmartFactory Reporting Solution. It’s a real-time visualization of factory operations and KPIs, used to monitor important metrics that the manufacturing organization is concerned about and align planning and scheduling goals across the organization.
Ideally, this should be a decision support system for daily operations to make sure that they are effectively utilizing their resources and addressing areas that are impacting the fab, as well as identifying bottlenecks.
Michael: We have a preset definition of what they’re viewing. However, the customer defines which areas are most important to address in each shift based on some predetermined logic of where their bottleneck is in the factory. Different factories have different methods for identifying this condition.
The reporting then has a user focus. The high-level view is meant more for the manufacturing manager or director and then each of the module areas are for the section managers.
Michael: Real time just means that as transactions are happening in the factory’s MES those transactions are being replicated and displayed in the FactoryView application. The KPIs that are tied to those factory transactions also are changing as the transactions are occurring in the MES. For example, the movement of a lot from one step to the next would be considered a transaction; the logging of a tool of an equipment down would be a transaction, so would the logging of an equipment back up.
Any of the reports that have to do with real time status of tools as well as factory metrics having to do with movement of material in the factory would be impacted by the real time nature of this application.
Michael: That’s a great question! It’s key to understand that this doesn’t require an industrial engineer, IT, or developer to create the actual dashboard and maintain it. FactoryView comes already developed, so the industrial engineer or IT can use it more as a tool to make decisions and help align the manufacturing organization. It takes the reporting aspect out of the IT and IE role to enable them to focus more on using that information to make better decisions for the factory.
I will also say, most customers do have something in terms of factory reporting; they all need to understand at a high level what’s going on in their factory and are driving towards a goal. But creating these reports is cumbersome for the staff who do it—it takes a long time for them to develop and maintain them. Oftentimes, these reports also are siloed across various organizations and there are gaps. For operational reporting, there might be several reports that have the same factory KPIs but are calculated differently. Ultimately, there are certain reports that factories don’t have that FactoryView does, and there’s an advantage in having that single source of truth for factory operational reports.
Michael: Our solution is built on years of experience deploying custom reporting solutions for customers, so we’ve been able to gain a lot of semiconductor-specific requirements. Often, what we’ve seen when we put this in front of customers is that they gain new insights, such as factory KPIs they didn’t think to track that may have come from a best known method (BKM) from another manufacturer in the industry. When they’re part of the roadmap for this reporting solution, they can pick up on the kind of industry BKMs for reporting instead of relying solely on the metrics they’ve been using.
Michael: I’d recommend engaging in some change management. There’s a certain way that the manufacturing organization has been looking at key metrics in their factory for many years, and this might change that view. Their daily stand-up meeting may change a little bit and may incorporate this report, and that will take some learning on how to use the application. There’s definitely an early change management cycle that goes on because of this.
In addition to change management, I would also say an important early step is to verify the metrics. With every deployment, you need to gather all the MES data and make sure the application works for the customer, ensuring that each of the metrics aligns with the way that the customers have defined them.
Michael: Yes, since it’s built on the same common data model as all our EngineeredWorks solutions, many of the inputs and the factory KPIs that we are producing in this solution would be shared across the other solutions. For instance, we would be calculating the same throughput statistic for scheduling as we would in FactoryView. When a tool is up in FactoryView, it would also be considered up in the scheduling solution and we would be considering the same tool list as the scheduling solution.
When you do a deployment of the reporting solution, it actually sets you up quite nicely for a scheduling solution deployment because many of the key pieces of data that you need for the reporting solution are also needed in scheduling. It cuts down on deployment time.
Up next
About the Authors
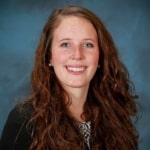
Samantha is the Global Product Manager overseeing SmartFactory AI™ Productivity, Simulation AutoSched® and Simulation AutoMod®. Prior to joining Applied Materials Automation Product Group Samantha was Manager of Industry 4.0 at Bosch, where she also was previously a Data Scientist. She also has experience as a Research Associate for the Geographic Information Science and Technology Group of Oak Ridge National Laboratory. She holds a M.S. in Mathematics from the University of Tennessee, Knoxville, and a B.S. in Mathematics from University of North Georgia, Dahlonega.

In his current role, Michael drives road map initiatives for Workflow Automation and Factory Analytics offerings to meet the growing needs of Semiconductor customers worldwide. Prior to his current role, Michael honed his expertise as an Industrial Engineer in the semiconductor industry, where he helped drive digital transformation and I4.0 initiatives for a 150mm/200mm front-end fab. With a passion for technology and a commitment to driving innovation, Michael continues to work with customers from around the world in advancing manufacturing capabilities and operational efficiencies.