Sam: Now that I understand FactoryView better, let’s bring AI into the discussion. Can you walk me through how someone is currently using FactoryView, and how their experience or outcomes might change if AI could start offering intelligent suggestions along the way?
Michael: Currently, the user monitors and interprets the factory KPIs. Based on what they’re seeing in the application around those, they’ll decide what area to focus on or where to deploy resources at any given time. Decision-making is currently a manual process. We’re just providing a decision support system.
Where AI would add significant value would be in the quality of the decision itself. Often, when humans are making decisions, it causes more variation because they don’t understand the factory’s overall dynamics. They might be very focused on a specific problem in a specific area, but they don’t know the impact that local optimization may have on the factory’s performance. It would be ideal if instead you used AI to take a holistic view of the factory and determine the best action for it. This would avoid the kind of local optimizations that can sometimes make a factory run very inefficiently.
Sam: Got it—so beyond just explaining predictions, it’s also about making actionable recommendations. Switching gears a little, can you now walk me through how AI could enhance forecasting accuracy, especially when there’s limited or no historical data to work with?
Michael: Right now, FactoryView relies on statistical methods to make predictions based on historical data. That works well when we have a solid data foundation—but it becomes a challenge when the data is limited or unreliable, like with newly introduced devices in the factory. In those cases, traditional methods fall short because there just isn’t enough run history to make accurate forecasts.
That’s where AI can really add value. It can generate synthetic data by analyzing similar products, helping to fill those gaps and improve forecast accuracy. For example, in FactoryView, we have a chart that tracks each lot’s journey through the factory—from start to shipment. We can show the completed steps with real data but, for future steps, we currently rely on a basic prediction using historical averages. That approach breaks down for new devices with little to no history. AI could step in here to make smarter, more context-aware predictions—factoring in things like expected WIP, equipment performance, and patterns from similar products. That would make the system far more reliable, especially in dynamic or fast-changing production environments.
Michael: I’d say, in a semiconductor factory there are too many variables for humans to contemplate whether the decision they’re making is the best decision. What often happens when people make what they think is an optimal decision in a semiconductor factory is that they overlook a number of variables; they’re only looking at a subset of all the variables in play. Even if there were a report that could provide them with all the necessary variables, I think it would take a human a very long time to make that determination, if they could do it at all.
Michael: To me, it would be a stepwise approach at first, where it starts by just suggesting and explaining its rationale for the suggestion. I think it would go through some level of scrutiny and training from the manufacturing operations team, because there would be things the AI isn’t aware of yet and needs feedback from that team to learn. Once the manufacturing team starts to trust these more informed suggestions, then I envision a factory would start to allow it to not just suggest, but to act. This could be making MES changes, handling certain alerts in an automated fab, sending material handling systems to move material to certain areas, and such.
Conclusion
About the Authors
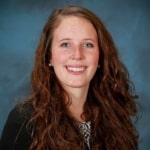
Samantha is the Global Product Manager overseeing SmartFactory AI™ Productivity, Simulation AutoSched® and Simulation AutoMod®. Prior to joining Applied Materials Automation Product Group Samantha was Manager of Industry 4.0 at Bosch, where she also was previously a Data Scientist. She also has experience as a Research Associate for the Geographic Information Science and Technology Group of Oak Ridge National Laboratory. She holds a M.S. in Mathematics from the University of Tennessee, Knoxville, and a B.S. in Mathematics from University of North Georgia, Dahlonega.

In his current role, Michael drives road map initiatives for Workflow Automation and Factory Analytics offerings to meet the growing needs of Semiconductor customers worldwide. Prior to his current role, Michael honed his expertise as an Industrial Engineer in the semiconductor industry, where he helped drive digital transformation and I4.0 initiatives for a 150mm/200mm front-end fab. With a passion for technology and a commitment to driving innovation, Michael continues to work with customers from around the world in advancing manufacturing capabilities and operational efficiencies.