EV(電気自動車)への急速な移行に伴い、30年以上にわたり大きな変化のなかった従来型のバッテリーメーカーは、需要に応じて新たな工場を建設し、しばしば本拠地から遠く離れた場所に巨額の投資を行っています。IoTの接続が進むこの時代では、過去と同じ方法でオペレーションを続けると、情報過多に陥る可能性があります。したがって、エビデンスに基づいてオペレーションに関する有意義な事実を抽出することが重要です。
迅速な問題解決が求められる中、リアルタイムでの知識発見が鍵となります。その一例が、長年の属人的な知識を、異なるデータソース間の因果関係や関連性を特定することで置き換えることです。本ブログでは、統計的工程管理(SPC)を、故障検出(FD)を通じた装置性能センサーデータとの関係に基づいて分析・特徴づけます。
プロセス理解の深化
SPCデータ(例:電極工程における塗布厚みの変動)と装置センサーデータ(例:塗布ヘッドの温度、ローラー速度、振動パターン、圧力)との関係を分析することで、装置の状態がプロセス結果にどのように影響するかを深く理解できます。
この統合分析により、個別のデータストリームを単独で見ているだけでは見逃されがちな隠れた相関関係を明らかにできます。たとえば、装置の微細な振動変化がコーティング厚さの変動増加と相関している場合があります(図1参照)。FDでは通常、アラーム監視のための限界値を設定し、特定のレシピにおける標準状態を理解します。しかし、単変量分析(UVA)の範囲内の変動も、視覚測定とセンサーデータの相関戦略においては意味を持ちます。リアルタイムで診断を下す能力は自動化システムで実現可能ですが、人間が迅速に電極のリスクを特定・緩和するのは困難です。
データに基づく意思決定
予知保全
装置センサーデータ(温度、振動、圧力、電流など)は、大きな故障が発生する前に微細な変化を示すことがあります。経験豊富な製造業者では、これは現場で長年働いてきたチームの属人的な知識として現れます。企業が生産を拡大し、新工場を建設し、新たな従業員(しばしば海外)を雇用する中で、この属人的知識を新しい施設で再現することが課題となります。このデータをSPCデータと重ね合わせることで、装置の問題の初期兆候を特定し、本社と同等またはそれ以上の歩留まりで新工場を運営することが可能になります。
予知保全により、予防的な保守スケジューリングが可能となり、突発的なダウンタイムを最小限に抑え、装置の稼働率を最大化できます。問題が深刻化する前に対処することで、装置の寿命を延ばし、保守コストを削減できます。
まとめ
バッテリー製造が進化を続ける中で、SPCとFDの相関分析の役割はますます重要になります。この統合アプローチを採用するメーカーは、今日のEV市場の要求に自信と柔軟性を持って対応できるでしょう。
SmartFactory Process Controlは、製造装置とプロセスの挙動を明示的に可視化し、カスタマイズされた継続的かつ自動化された調整を可能にします。これにより、バッテリーメーカーは高い品質基準を維持しながら、高速ロールと高効率を実現できます。SmartFactoryは、半導体業界で培った最先端の実践をバッテリー製造に提供し、生産歩留まりと効率の最大化を目指しています。
著者について
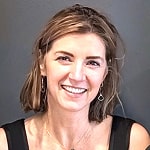
バッテリー製造と戦略的アライアンスを担当するセグメントマネージャーです。Applied Materials Automation Product Groupに入社する前は、Panasonic Connectでスマートファクトリーパートナーシップのマネージャーとして、生産性、自動化、MES、保守ソフトウェアの導入を担当していました。また、DePaul大学でファイナンスのMBA、イリノイ工科大学で機械工学の学士号を取得しています。
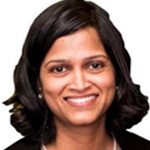
半導体業界で15年以上の経験を持っています。Applied Materialsに入社する前は、Micron Technologyでプロセスエンジニアとして、そしてその後はシニア品質エンジニアとして勤務していました。彼女は7年前に品質ソリューションアーキテクトとしてAppliedに入社し、現在、グローバルプロダクトマネージャーとして、SmartFactory SPC3Dを担当しています。これは、プロセスが仕様内に収まっているかどうかを統計的に判断し、製品の歩留まりを向上させるための高度なプロセス制御(APC)エンジンです。彼女はオクラホマ州立大学で機械工学の修士号を、インド・テランガーナ州ハイデラバードにあるオスマニア大学で機械工学の学士号を取得しています。